Sika® Permacor®-3326 EG H
2-komponentige, lösemittelarme, eisenglimmerhaltige Beschichtung auf Epoxidharzbasis. Die Beschichtung ist mechanisch widerstandsfähig und chemisch belastbar sowie abrieb-, stoss- und schlagfest. Rissüberbrückung 3 mm (Lamminataufbau) nach SVTI.
- Hohe Beständigkeit gegen Wasser, aggressive Abwässer und viele Chemikalien,insbesondere Salzlösungen und bei biologischen Prozessen auftretende Säuren
- Hoher Diffusionswiderstand
- Sehr gute Haftfestigkeit auf mineralischen Oberflächen
- Hohe Sicherheit für Verarbeiter durch Porenprüfbarkeit der Beschichtung
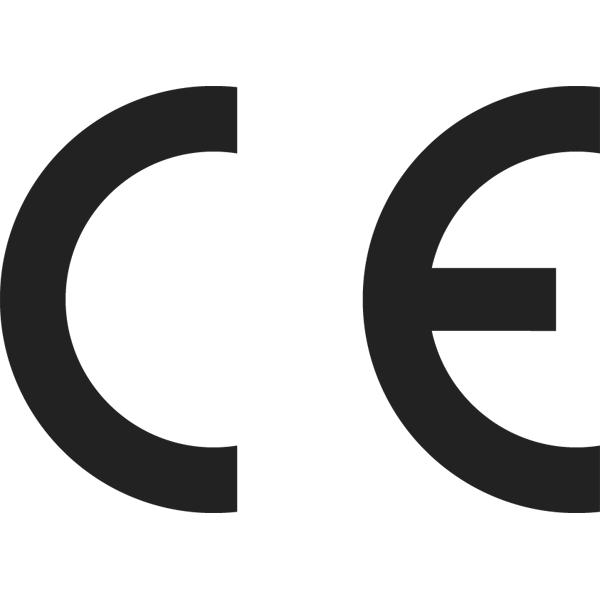
Anwendung
- Hervorragend geeignet für den Korrosionsschutz direkt medienbeanspruchter Oberflächen aus Beton.
- Hauptsächlich eingesetzt für Faulschlamm-Behälter, Rotte-Container, Brauchwasser-, Abwasser-, Chemikalien- und Ballasttanks sowie Kühlwasserleitungen oder Biogasanlagen.
- Geeignet als robuster Korrosionsschutz im atmosphärischen Industriebereich, z. B. für Rohrbrücken, Abfüllstationen, Behälter- und Rohraussenflächen, Maschinen und Apparate.
Vorteile
- Hohe Beständigkeit gegen Wasser, aggressive Abwässer und viele Chemikalien,insbesondere Salzlösungen und bei biologischen Prozessen auftretende Säuren
- Hoher Diffusionswiderstand
- Sehr gute Haftfestigkeit auf mineralischen Oberflächen
- Hohe Sicherheit für Verarbeiter durch Porenprüfbarkeit der Beschichtung
Verpackung
Komp. A: | 13 kg |
Komp. B: | 3 kg |
Komp. A + B: | 16 kg Fertigmischung |
Farbe
Aussehen: | Matt |
Farbe: | Kieselgrau, ~ RAL 7032 |
Produktedetails
UMWELTINFORMATIONEN
IBU Umwelt-Produktdeklaration (EPD)
PRÜFZEUGNISSE
- CE-Kennzeichnung und Leistungserklärung nach EN 1504-2: Oberflächenschutzprodukt - Beschichtung
- SVTI Schweizerischer Verein für technische Inspektionen, Wallisellen (CH): Zertifikat Produkte-Prüfung nach KVU - KVU-Nr. 222.011
- Nachweis der chemischen Beständigkeit gegen biogene Schwefelsäure (Kat. XWWW4/XBSK) gemäss DIN 19573 und DIN EN 13529
Haltbarkeit
Im ungeöffneten Originalgebinde: 24 Monate ab Produktionsdatum
Lagerbedingungen
Lagertemperatur zwischen +5 °C und +30 °C. Kühl und trocken lagern.
Dichte
~ 1.9 kg/l
Feststoffgehalt nach Gewicht
~ 88 %
Feststoffgehalt nach Volumen
~ 75 %
Chemische Beständigkeit
Je nach Medium
Bitte Technischen Verkaufsberater der Sika Schweiz AG kontaktieren.
Die Dauerbeständigkeit gegenüber ozonhaltigen Medien ist nicht gegeben.
Thermische Beständigkeit
Trockene Hitze: | ~ +100 °C |
Bei höheren Temperaturen bitte Technischen Verkaufsberater der Sika Schweiz AG kontaktieren.
Applikation
Mischverhältnis
Komp. A : B: | 100 : 23 (Gew.-Teile) |
Verdünnung
Sika® Verdünnung E+B
Materialtemperatur
Min. +10 °C
Relative Luftfeuchtigkeit
Max. 85 %
Max. 80 % bei Behältern, ausser die Objekttemperatur ist deutlich höher als die Taupunkttemperatur.
Taupunkt
Keine Kondensation!
Die Untergrundtemperatur während der Applikation und Aushärtung muss mindestens 3 °C über dem Taupunkt liegen.
Untergrundtemperatur
Min. +10 °C
Untergrundfeuchtigkeit
Max. 4 % | (CM-Messung) |
Topfzeit
Temperatur | Zeit |
+20 °C | ~ 90 Minuten |
+30 °C | ~ 45 Minuten |
Aushärtezeit
Mechanisch und chemisch voll belastbar: | 7 Tage (+20 °C) |
Prüfungen an der fertigen Beschichtung sollen erst nach der genannten Schlusstrockenzeit durchgeführt werden.
Porositätsprüfung
Mit geeignetem Hochspannungsgerät, z. B. Fischer-Poroscope® HV20D mit Flachelektrode (Gummizunge). Prüfspannung 5 Volt pro μm Schichtdicke.
Durch mehrfache Hochspannungsprüfung kann sich die Durchschlagsfestigkeit der Beschichtung vermindern. Bei Wiederholungsprüfungen ist das zu berücksichtigen.
Wartezeit zwischen den Arbeitsgängen
Wartezeit
Min. 12 Stunden, max. 48 Stunden1. | (+20 °C) |
- Beim Einsatz als Innenbeschichtung.
Bei längerer Zwischentrocknungszeit ist Anstrahlen der Beschichtung erforderlich.
Überarbeitung
Sika® Permacor®-3326 EG H ist nur mit sich selbst überarbeitbar, bei atmosphärischer Beanspruchung auch mit Sika® Permacor®-2330 und Sika® Permacor®-2230 VHS.
Vor dem nächsten Arbeitsgang sind die evtl. entstandenen Verunreinigungen zu entfernen.
Trockenzeit
Handtrocken: | ~ 4 Stunden (+20 °C) |
Begehbar: | ~ 12 Stunden (+20 °C) |
Verbrauch
Theoretischer Materialverbrauch/Theoretische Ergiebigkeit ohne Verlust für mittlere Trockenschichtdicke
Trockenschichtdicke: | 250 µm |
Nassschichtdicke: | 330 µm |
Verbrauch: | 0.633 kg/m2 resp. 1.58 m2/kg |
Die angegebenen Schichtdicken berücksichtigen nicht die Korrekturfaktoren für raue Oberflächen gemäss ISO 19840.
UNTERGRUNDVORBEREITUNG
Beton, Zementputz
Die zu beschichtenden Oberflächen müssen den bautechnischen Normen entsprechen, tragfähig, fest und frei von verbundstörenden Stoffen sein.
Die Oberflächenzugfestigkeit nach DIN 1048 soll im Mittel mindestens 1.5 N/mm2 betragen und darf mit dem kleinsten Einzelwert 1.0 N/mm2 nicht unterschreiten. Bei starker mechanischer Belastung ist der Sollwert im Mittel 2.0 N/mm2 und der kleinste Einzelwert 1.5 N/mm2.
Es sind geeignete, dem System angepasste, Vorbeschichtungen einzusetzen.
Die entsprechenden Überarbeitungszeiten sind einzuhalten.
MISCHEN
Vor dem Mischen Komp. A und Komp. B maschinell aufrühren (langsam beginnen und bis max. 300 U/Min.).
Komp. A und Komp. B vor der Verarbeitung im vorgeschriebenen Mischungsverhältnis vorsichtig zusammengeben.
Um Spritzer oder gar ein Überschwappen der Flüssigkeit zu verhindern, die Komponenten mit einem stufenlos verstellbaren, elektrischen Rührgerät kurze Zeit mit geringer Drehzahl durchmischen. Anschliessend die Rührgeschwindigkeit zur intensiven Vermischung auf max. 300 U/Min. steigern. Die Mischdauer beträgt min. 3 Minuten und ist erst dann beendet wenn eine homogene Mischung vorliegt.
Gemischtes Material in ein sauberes Gefäss umfüllen (umtopfen) und nochmals kurz, wie oben beschrieben, durchmischen.
APPLIKATION
Die angegebene Trockenschichtdicke wird mit dem Airless-Spritzverfahren erreicht. Das Erlangen einer einheitlichen Schichtdicke sowie gleichmässiger Optik ist vom Applikationsverfahren abhängig. Im Allgemeinen führt das Spritzverfahren zum besten Ergebnis. Die Zugabe von Lösemittel reduziert die Standfestigkeit und die Trockenschichtdicke. Im Streich- oder Rollverfahren sind für die geforderte Schichtdicke je nach Konstruktion, örtlicher Gegebenheiten und Farbton weitere Arbeitsgänge vorzusehen. Zweckmässigerweise ist vor dem Beginn der Beschichtungsarbeiten mittels einer Probefläche vor Ort zu prüfen, ob das gewählte Applikationsverfahren mit dem vereinbarten Produkt im Ergebnis den Erfordernissen entspricht.
Streichen oder Rollen
Beim Streichen oder Rollen ist eine Sollschichtdicke von max. 150 μm erreichbar. Evtl. ist ein zusätzlicher Arbeitsgang notwendig.
Gegebenenfalls max. 5 Gewichts-% Sika® Verdünnung E+B zugeben.
Airless-Spritzen
Pumpe: | Leistungsfähiges Airlessspritzgerät |
Spritzdruck in der Pistole: | Min. 180 bar |
Siebe: | Entfernen |
Spritzdüse: | ≥ 0.38 mm |
Spritzwinkel: | z. B. 50° |
Spritzschläuche: | 3/8" |
Vor der Spritzpistole: | 1/4", ~ 2 m |
Materialtemperatur: | Min. +15 °C |
Gegebenenfalls max. 5 Gewichts-% Sika® Verdünnung E+B zugeben.
GERÄTEREINIGUNG
Sika® Verdünnung E+B